E-ONE Trucks
E-ONE is the pioneer—the leader.
Founded in 1974 by an industrial engineer with a revolutionary concept, E-ONE designed and manufactured the first modular, extruded aluminum fire truck and body.
The innovative E-ONE structure has undergone extensive successful testing well beyond industry standards for crush weight, providing first responders with the highest safety and dependability. E-ONE is the global full-spectrum manufacturer of pumpers, tankers, aerial ladders and platforms, rescues, industrials and ARFFs.
E-ONE, a full-spectrum builder of fire apparatus, is the pioneer and recognized leader in extruded aluminum and stainless steel construction. With advanced engineering, fully integrated manufacturing and a highly engaged dealer network, the E-ONE team proudly delivers strength through excellence.
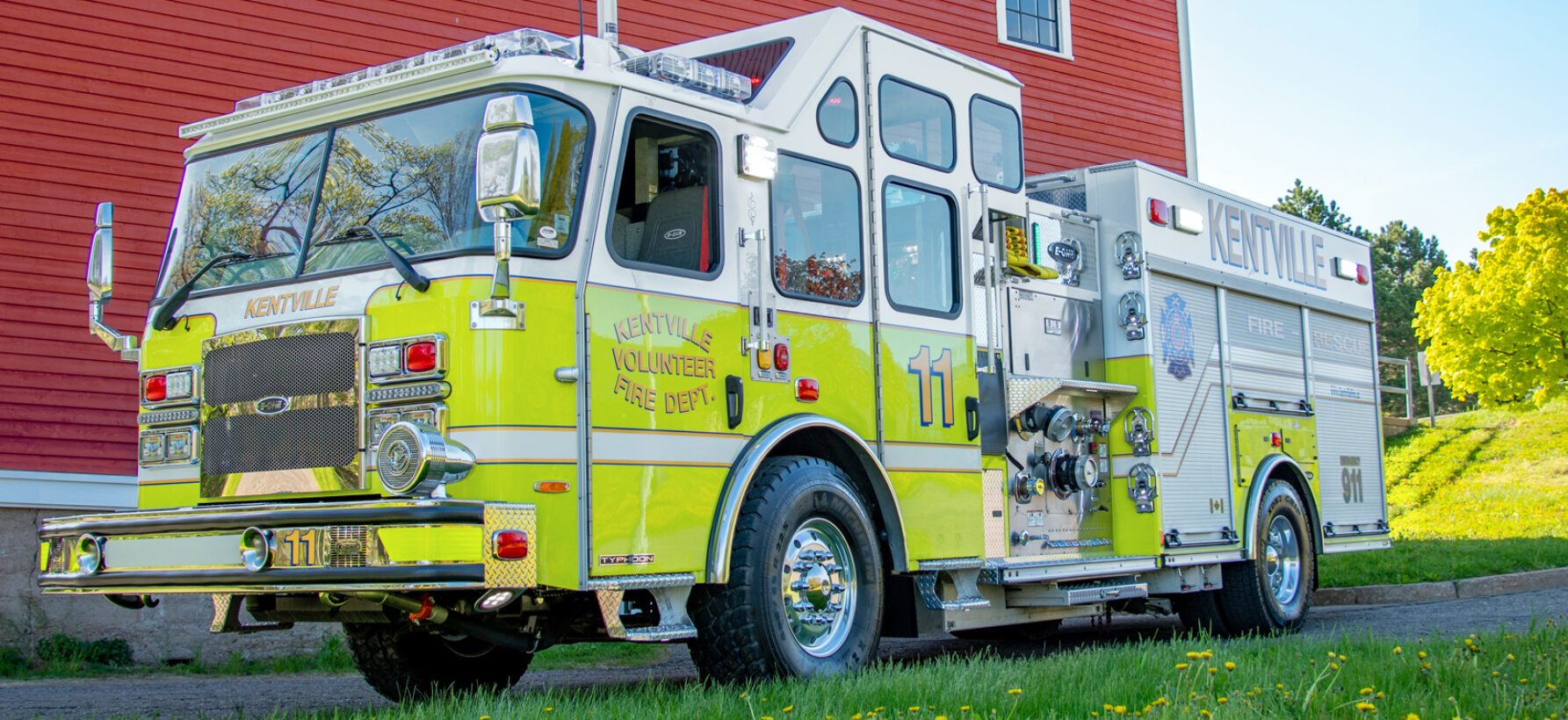
Custom Fire Truck Chassis
We offers three custom chassis – Cyclone®, Typhoon® and the FC-94.
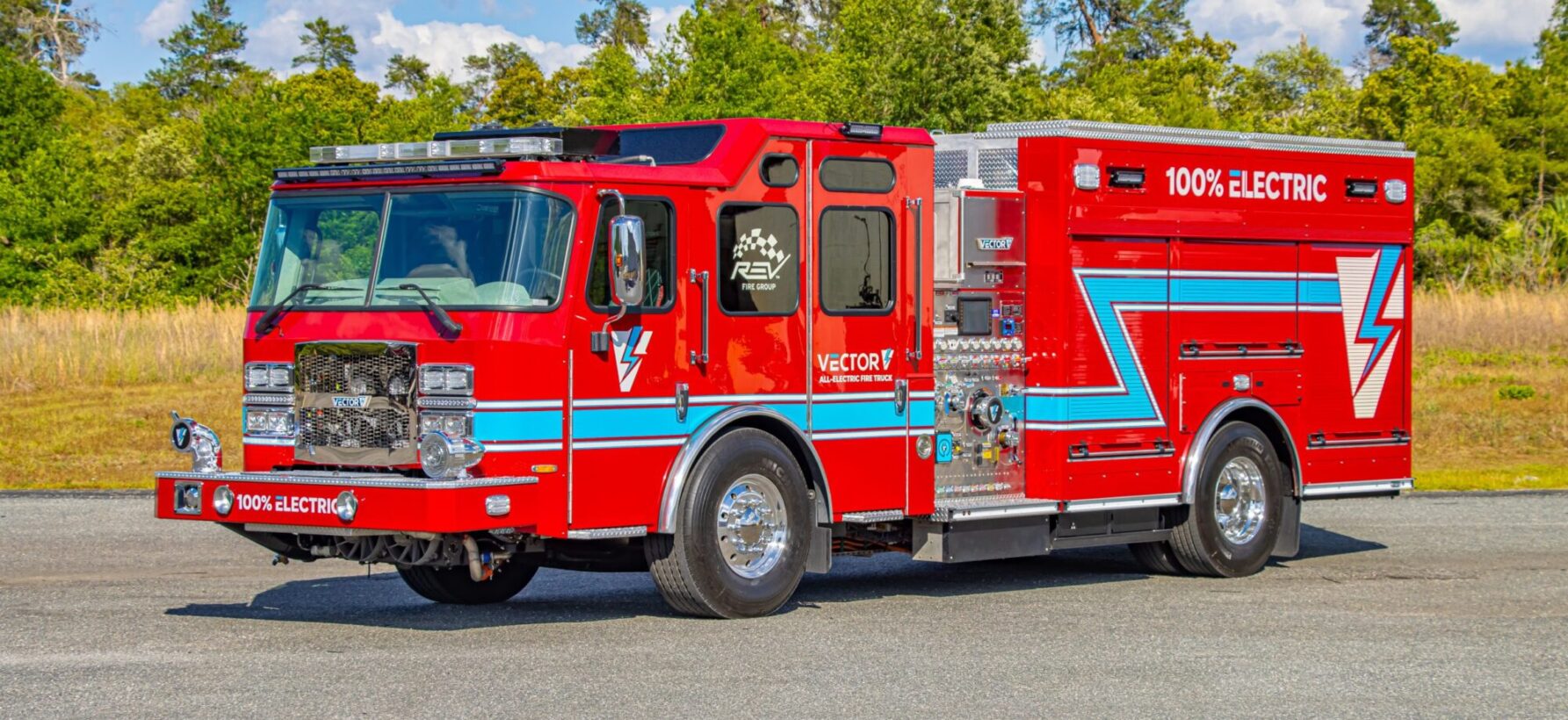
Electric trucks
Energize your firefighting capabilities and protect your crews and the environment from air and noise pollution with Vector, the first North American-style fully electric fire truck.
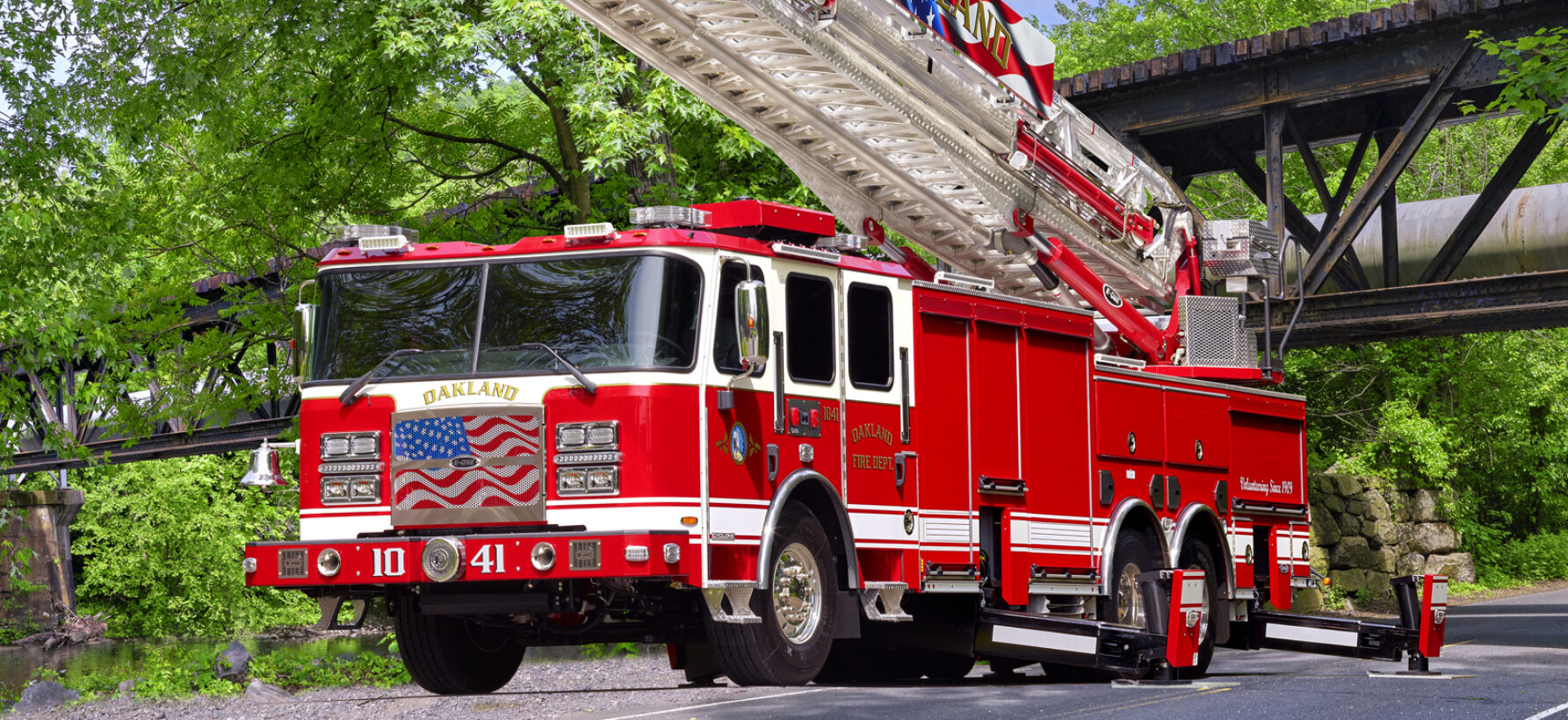
Platforms
Versatility from the platform up! E-ONE’s platforms are all-aluminum for strength and offer dual front gates and a front console that improves visibility.
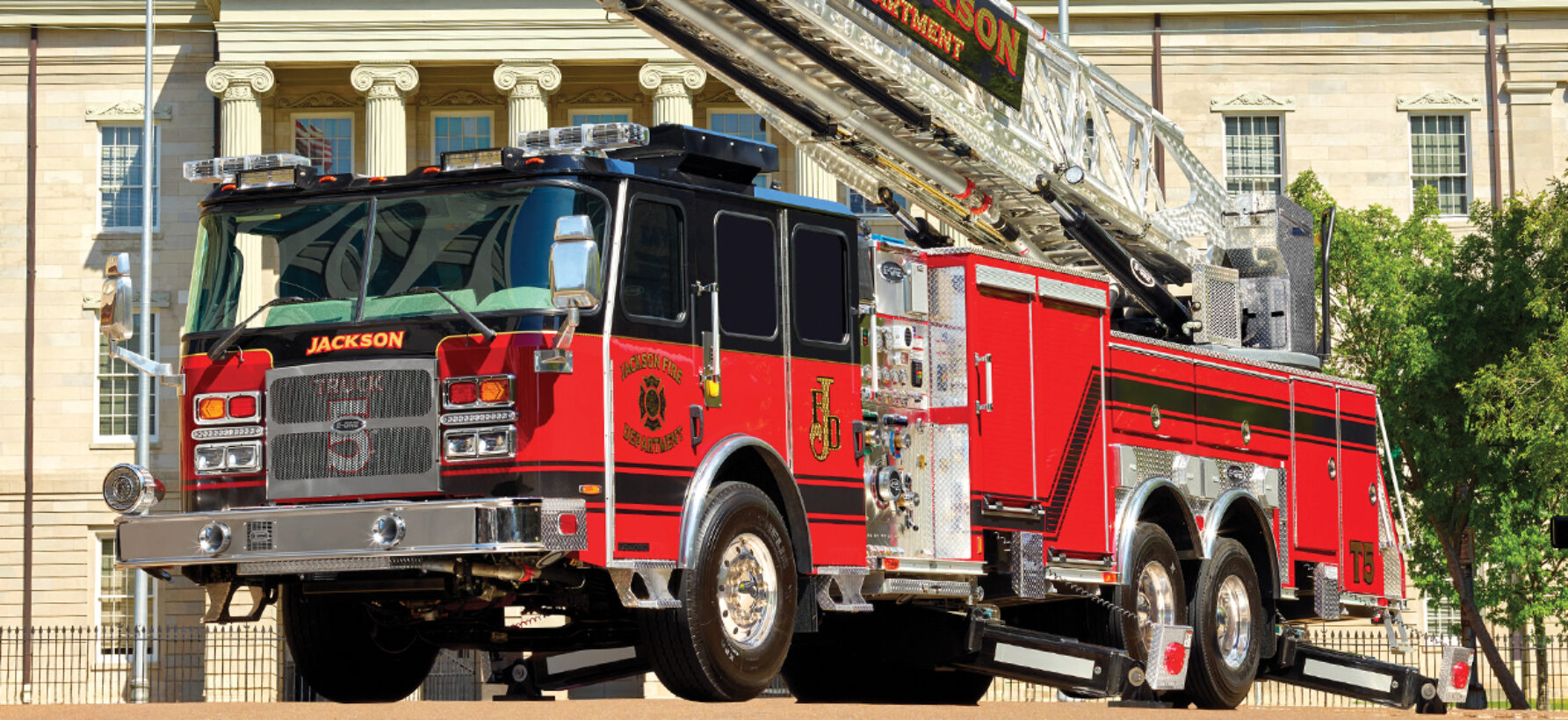
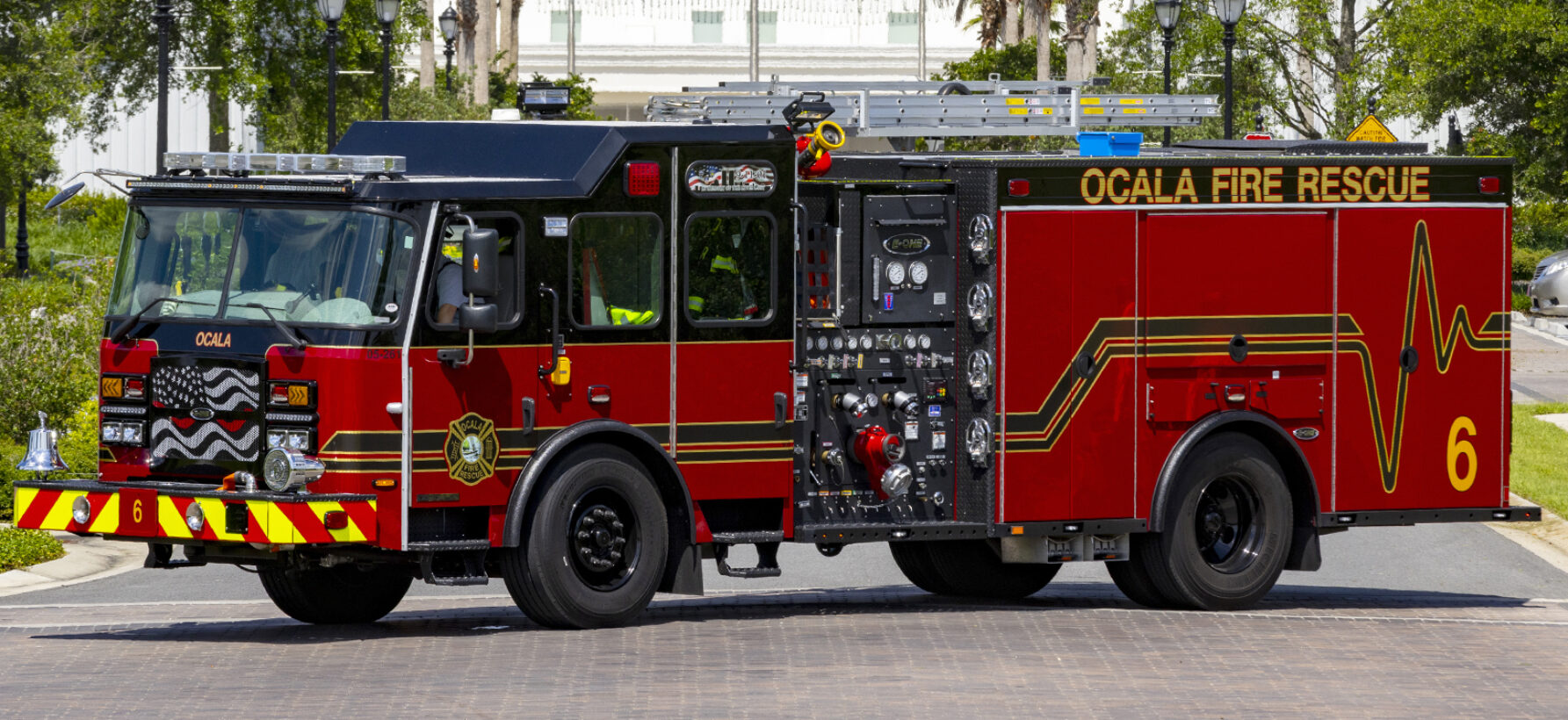
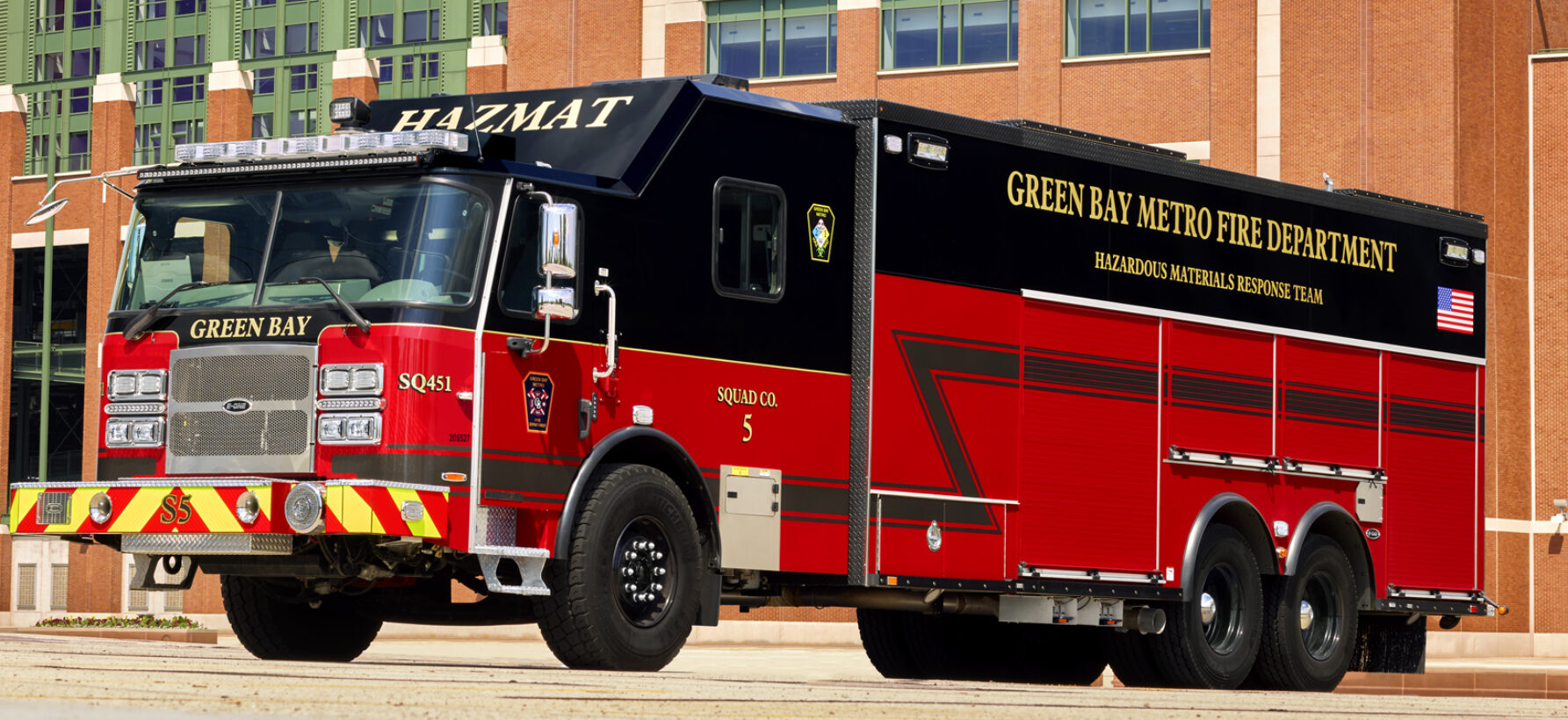
Rescue units
Every E-ONE rescue project is a unique endeavor which starts with you, the rescue operators.
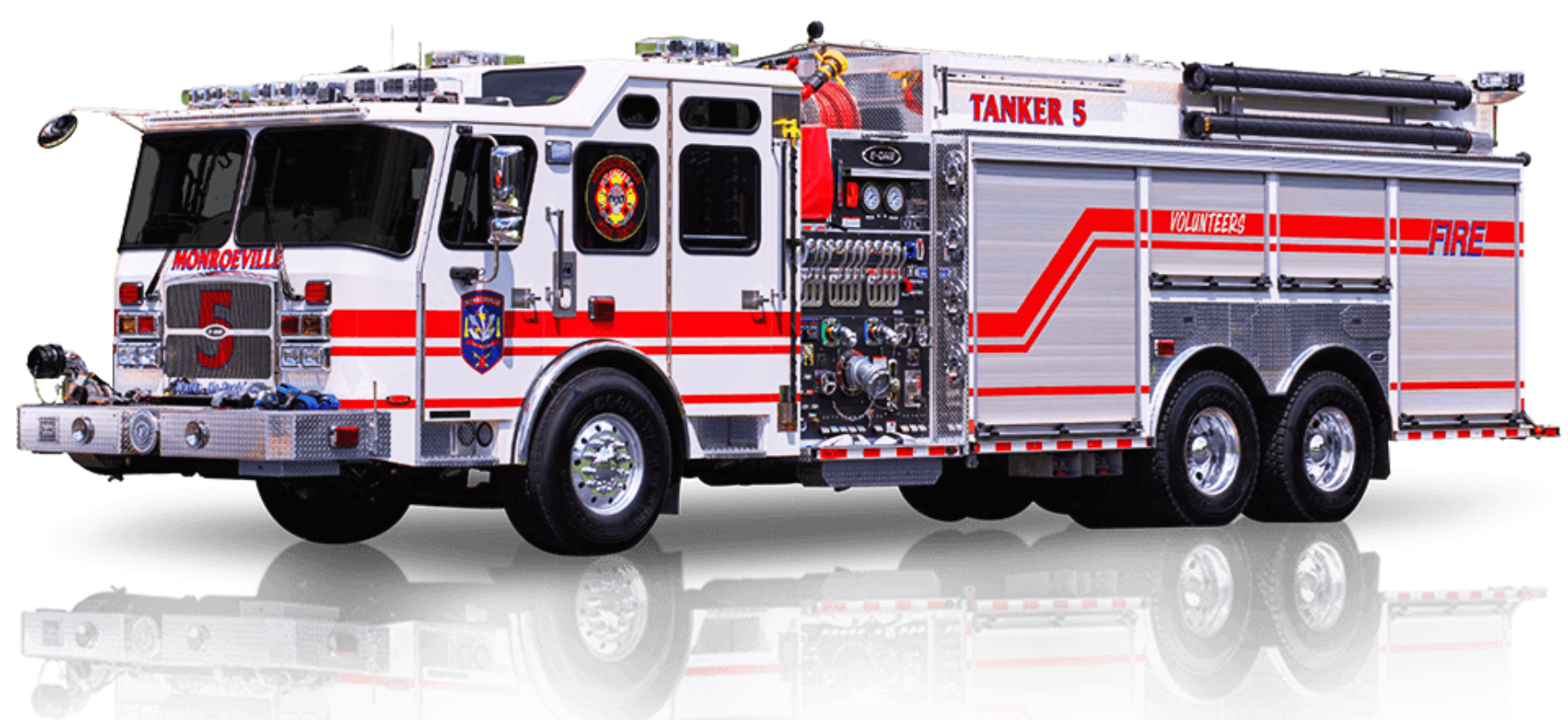
Tankers
E-ONE® Tankers were designed from the ground up to deliver the maximum amount of water to the scene with the minimum amount of personnel.
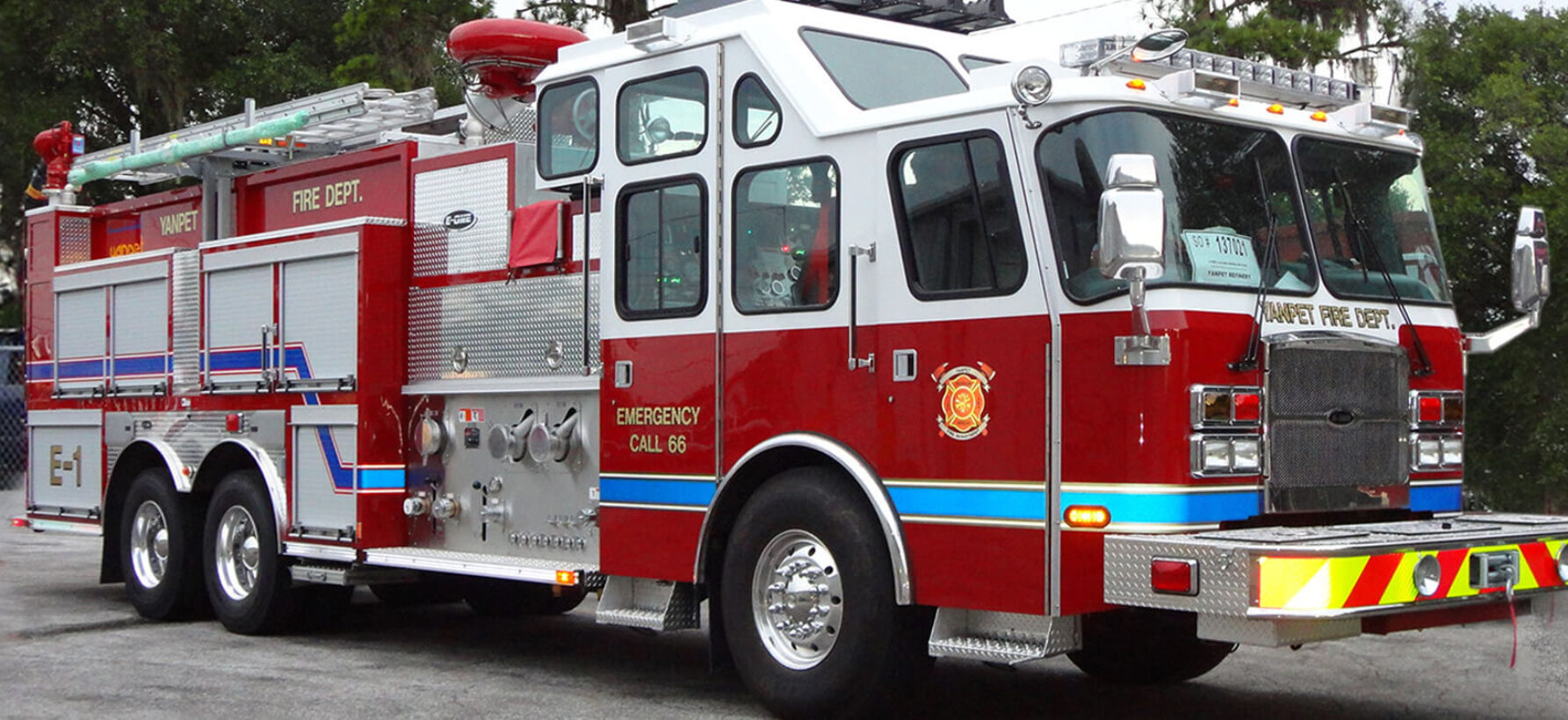
Industrials
With more than 28,000 first responder vehicles in active service throughout North America and 80 countries around the world, what really sets our industrial pumpers apart is the versatility, durability and quality you’ll receive from your E-ONE® industrial pumper.
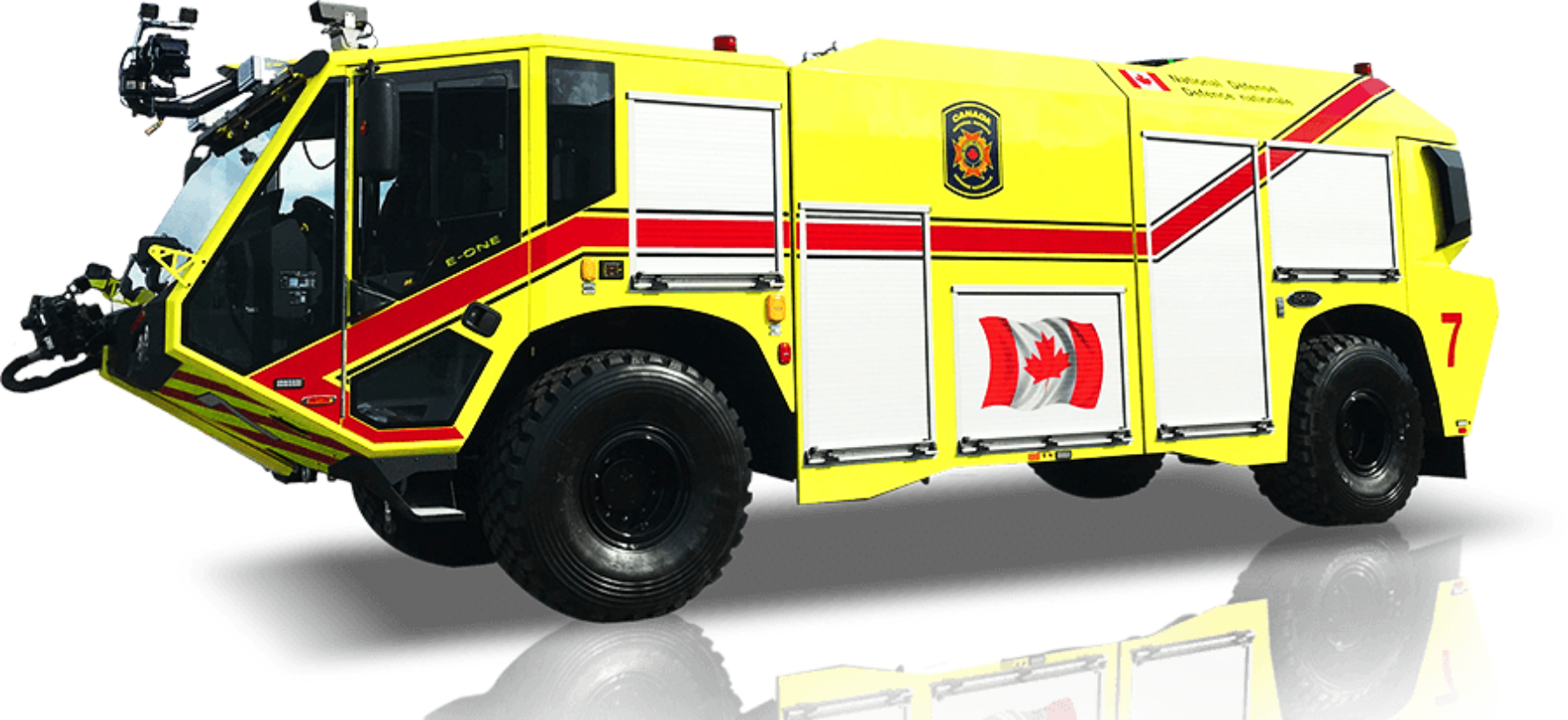
You want to learn more about our trucks?
Want to learn more about our trucks? Feel free to contact us by clicking the link below to get all the information you need! We’re here to answer all your questions and provide you with the necessary details to find the truck perfectly suited to your needs. We look forward to assisting you in your search.
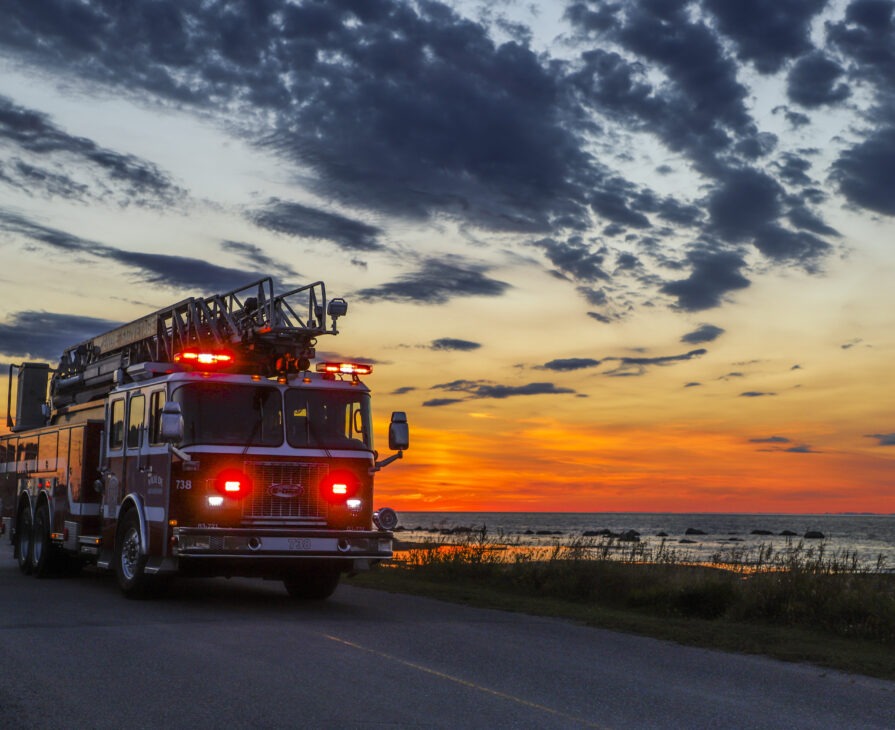